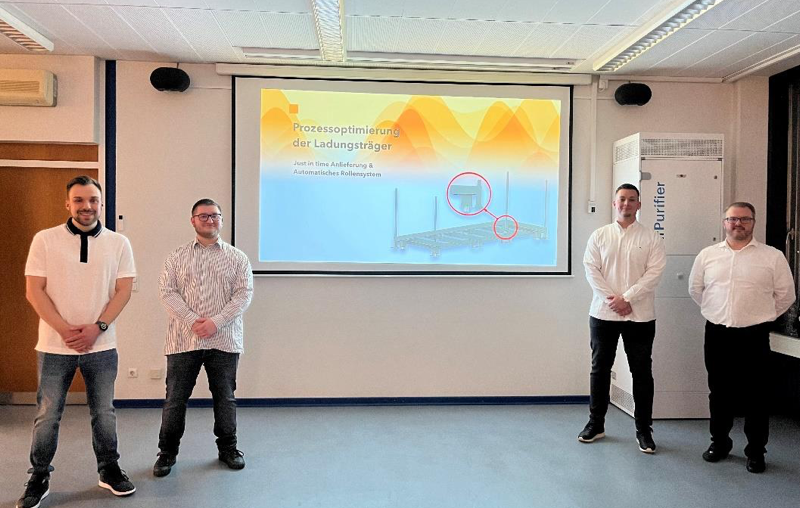
Technikerprojekt TMA4T1: „Entwicklung eines Multifunktions-Schweißvorrichtungssystems"
Am Ende der Projektphase haben wir erfolgreich unser Ziel erreicht, eine funktionsfähige Vorrichtung für die Firma „gym80“ zu konstruieren. Unsere Konstruktion trägt dazu bei, Arbeitsprozesse zu vereinfachen und zu verbessern. Dies ermöglicht es der Firma, Lagerkapazitäten und Ressourcen einzusparen, da keine zusätzlichen Materialien und Zeit für den Bau neuer Hilfsvorrichtungen benötigt werden. Die Flexibilität unseres Systems und die Erweiterung der Arbeitsbereiche von 12 auf 18 Mitarbeiter steigern die Produktivität des Unternehmens. Darüber hinaus leistet unser System einen wichtigen Beitrag zur Arbeitssicherheit bei der Firma „gym80“.
Es rentiert sich schnell und ist wirtschaftlich. Durch die Projektarbeit "Entwicklung eines Multifunktions-Schweißvorrichtungssystems" haben wir wertvolle Einblicke in unser zukünftiges Berufsfeld gewonnen und konnten die erlernten Methoden und das Fachwissen der letzten dreieinhalb Jahre anwenden (Projektteilnehmer siehe Bild unten)
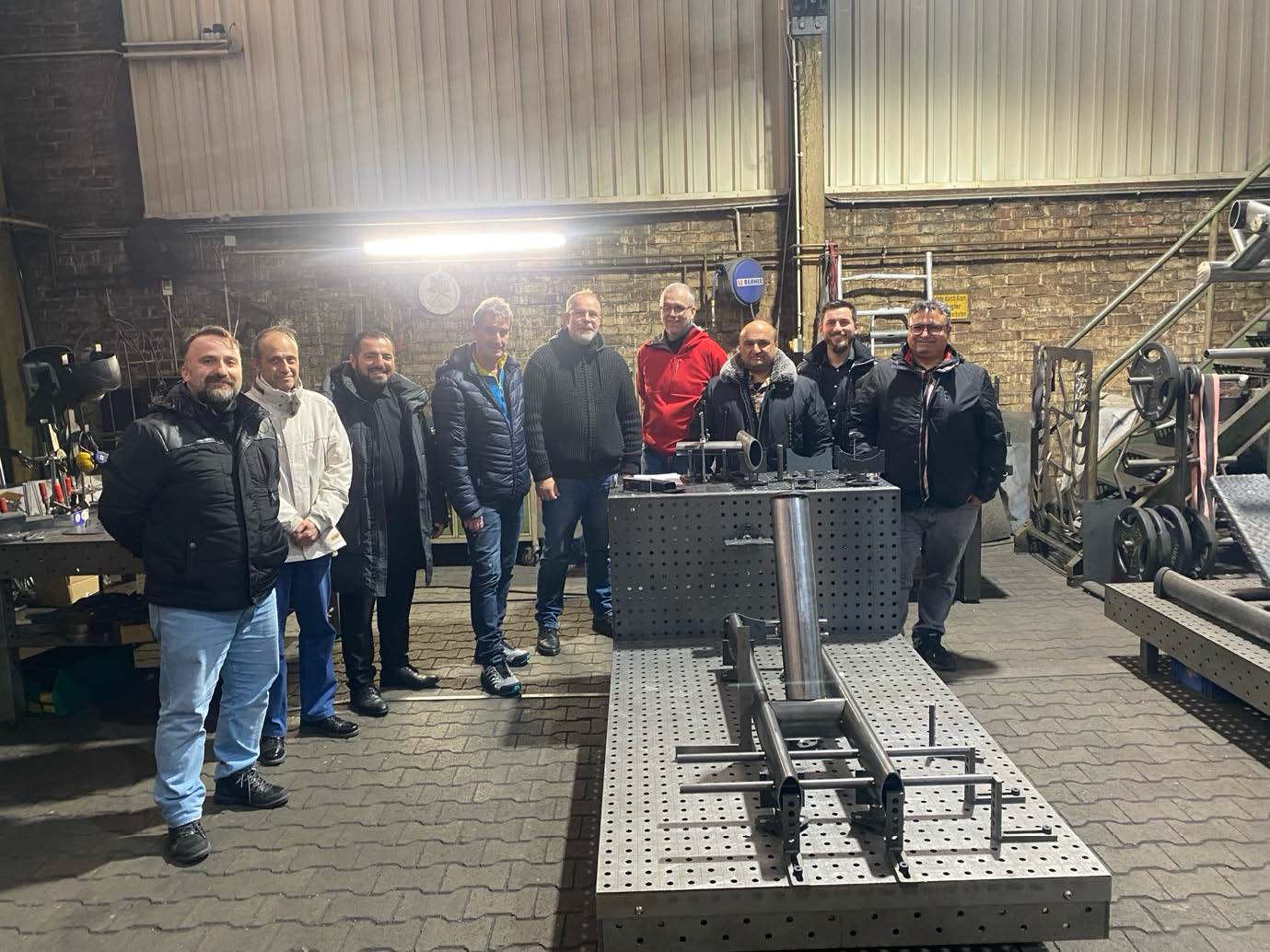
Zusammenfassung Projekt "Ladungsträger"
Die Firma Siemens hat uns den Auftrag gegeben, eine Prozessoptimierung in ihrem Unternehmen durchzuführen.
Prozessablauf:
Ein LKW-Trailer, der mit Ladungsträgern beladen ist, muss für die Montagehallen mobilisiert werden, damit diese in den verschiedenen Abteilungen von Hand bewegt werden können.
Dafür wird der Ladungsträger von dem Trailer von einem Gabelstaplerfahrer (Entlader) abgeladen und unter ein Schleppdach gefahren, dort wird der Ladungsträger von einem Monteur und einem Verteiler durch Aufsteckrollen mobil gemacht.
Von dort aus fährt der Verteiler den Ladungsträger in die Montagehalle.
Die Problemstellung bei diesem Prozessablauf:
Durch die sehr hohe Menge der Ladungsträger, die am Tag auf dem Siemensgelände abgeladen werden (ca. 250), entsteht im Bereich des Schleppdachs eine Engpassstelle, wodurch sich der Prozessablauf deutlich verzögert.
Um dies zukünftig abzustellen, kam uns die Idee, einen Mechanismus zu entwickeln, der sicherstellt, dass der Ladungsträger immer fest auf den Rollen sitzt. Die Rollen würden nur ausfahren, wenn sie wirklich gebraucht werden.
Diesen Mechanismus haben wir in der Projektphase erstellen und veranschaulichen können. Die automatisierten Rollen fahren durch das Anheben des Ladungsträgers aus und verkanten sich im Mechanismus und werden dadurch mobilisiert, sodass sie beim Abstellen in den Montagehallen von den Mitarbeitern bewegt werden können.
Wenn diese wieder durch einen Hubwagen oder Gabelstaplerfahrer angehoben werden, fährt der Mechanismus aus und verdreht sich anschließend in eine freigängige Nut, welche dem Ladungsträger ermöglicht, fest auf seinen eigenen Sockeln zu stehen. Nun kann der Ladungsträger direkt entladen und zur Montagehalle gefahren werden. Dadurch werden Personalkosten, Arbeitszeit und Mietfläche eingespart.
Die Arbeitssicherheit wurde erhöht, da kein häufiges Auf- und Absteigen auf den Gabelstapler mehr nötig ist. Der Monteur und der Verteiler können sich nicht mehr bei der Montage der Rollen verletzen, sowie die ungesunde Körperhaltung durch das Herausnehmen der Rollen aus der Gitterbox werden vermieden (Projektteilnehmer siehe Titelbild)